
Even large manufacturing firms in Uganda resemble groups of self-employed workers, which limits the gains to scaling these firms
Firms in developing countries are small and often consist of just a single self-employed person (Hsieh and Olken 2014). This fact has attracted the attention of policy-makers, leading to billions of dollars invested to help firms grow through many different development interventions, such as wage subsidies to hire more workers or capital grants (Quinn and Woordruff 2019, Jayachandran 2021). One key motivation behind these interventions is the belief that organising the economy into large firms may generate big productivity gains.
In new research (Bassi, Lee, Peter, Porzio, Sen and Tugume 2023), we challenge this widespread belief. We study the inner workings of manufacturing firms in Uganda and find that even individuals in the largest firms essentially operate as a group of self-employed workers who share the same production space. Due to this limited specialisation of labor, scaling up firm size does not improve the overall allocation of talent in the economy. Therefore, the productivity gains from larger firms can only come from other sources of economies of scale, such as fixed production costs.
Our findings have important implications for which interventions are best equipped to improve firm-level and aggregate productivity. Given the way firms are internally organised, supply-side interventions such as access to credit or wage subsidies may not be very effective: they would just move workers from being “self-employed” to being “self-employed within the firm”.
Measuring labour specialisation within firms
We surveyed a representative sample of 1,115 manufacturing firms in the carpentry, welding and grain milling sectors. These sectors account for a large share of manufacturing employment in Uganda and comprise both small and “large” firms (with about 10 employees). The key innovation of this survey is to measure “who does what” within each firm. To do so, we used diaries to collect time-use information separately for firm owners (“entrepreneurs”) and their employees. We know what tasks they perform and how much time they allocate to each task. This includes the time they each spend on various production tasks (e.g. sanding a door) and non-production tasks such as interacting with customers, supervising workers, or procuring inputs.
Stylised facts on labour specialisation in Ugandan manufacturing firms
We use our data to document a few stylised facts on the extent of labour specialisation and its variation with firm size. We first focus on carpentry and welding. Our main finding is that limited labour specialisation is a pervasive feature of how firms in these sectors operate in Uganda, even among firms that are large enough to specialise.
1. Employees perform similar production tasks: Figure 1 shows that 85% of employees perform each production task, for doors in carpentry (Panel a) and windows in welding (Panel b). This share decreases only slightly with firm size. We include – using red diamond markers - the hypothetical share of employees that would be allocated to each task if firms fully specialised their time in specific production tasks (minimising overlap between employees). The gap between observed and full specialisation shows that “horizontal” specialisation in production tasks is limited throughout the firm size distribution.
Figure 1: The allocation of production tasks by firm size
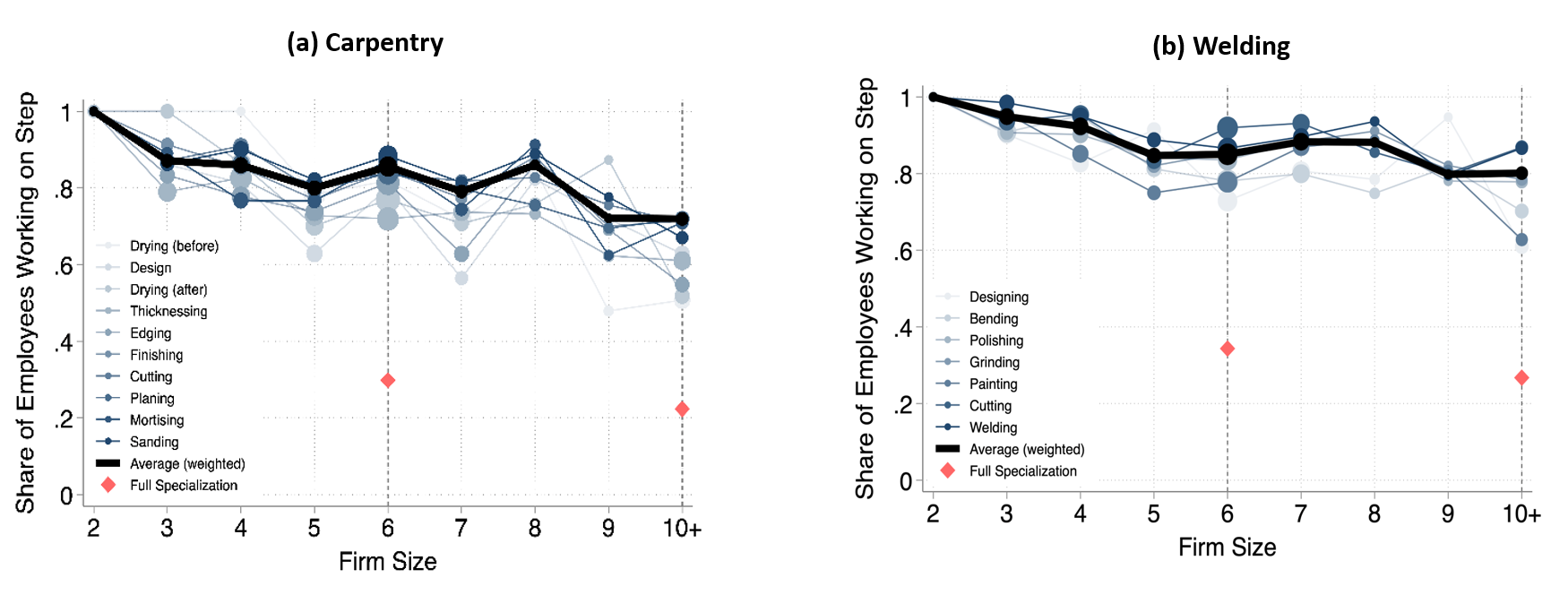
Notes: These figures report the share of employees working on each production step, where the steps in darker blue account for a larger share of production time. We also include – in black – the share of employees that perform the representative step. Red diamond markers represent the share of employees that would work on a production step under full specialisation.
2. Entrepreneurs are not fully specialised in non-production tasks: In Figure 2, we plot the share of individuals’ time allocated to non-production tasks by firm size, separately for employees (Panel a) and entrepreneurs (Panel b). The most skilled individuals in each firm specialise in non-production tasks, which we show to be more skill intensive. For example, entrepreneurs (who are more skilled) devote twice as much of their time to these tasks than employees. The difference between entrepreneurs and employees also increases among larger firms, which suggests that larger firms are more “vertically” specialised. However, this type of specialisation is still far from complete. We compare the observed share of entrepreneurs’ time with the share they would allocate if they fully specialised in non-production tasks (in pink). In firms with more than five employees, entrepreneurs spend only 50% of their time on non-production tasks, despite there being enough of these tasks to fill their workday.
Figure 2: Time allocated to non-production tasks by firm size
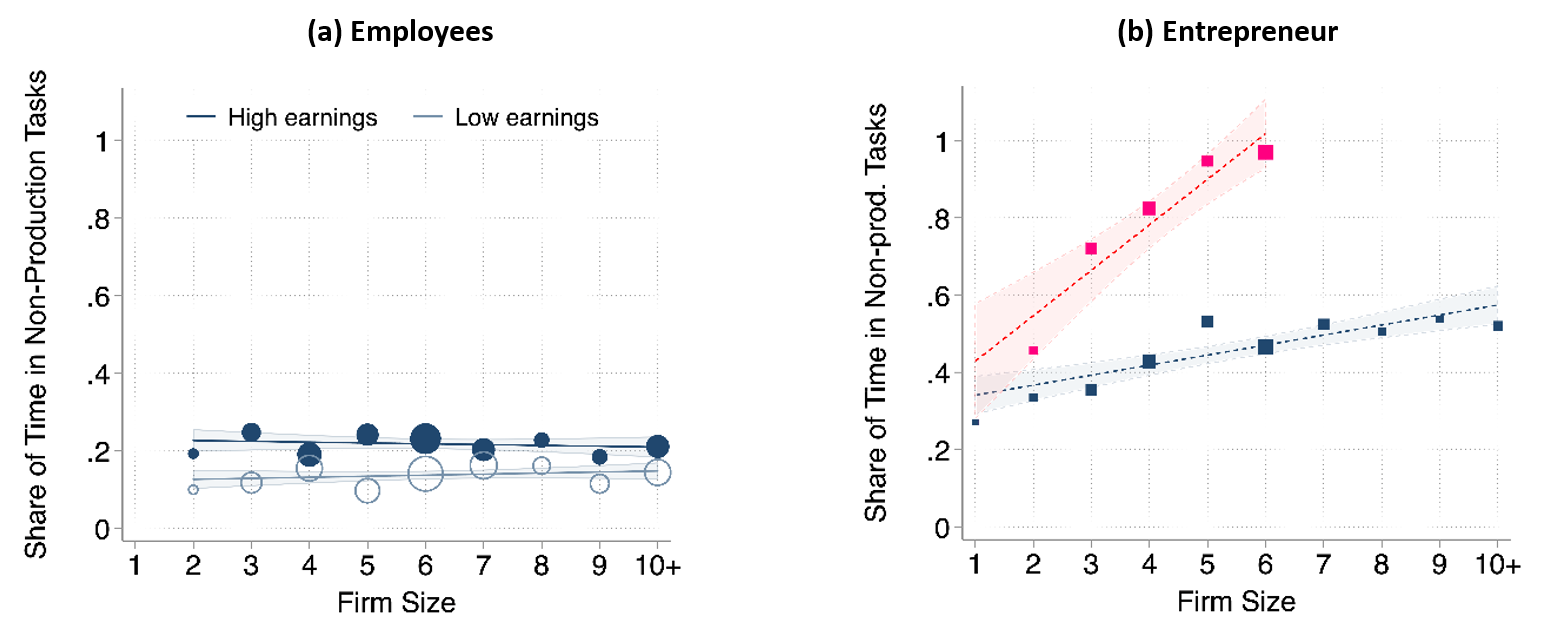
Notes: These figures report the share of time, excluding idle time, allocated to non-production tasks. Employees (in panel a) are classified as high or low earners within each firm (above or below the median). For entrepreneurs (in panel b) we also show the share of time they would devote under full specialisation (in pink). This is set to one for firms larger than size six.
Why don’t firms specialise?
Our data highlights that there is very limited specialisation among carpentry and welding firms – everyone does a bit of everything. So why don’t these firms specialise? While it is hard to pinpoint any one explanation, we uncover significant variation in the extent of specialisation across production sectors. Grain milling firms (and especially larger ones) tend to be much more specialised, with workers performing different production steps (Figure 3a) and entrepreneurs focusing on non-production tasks (Figure 3b). This difference is consistent with the notion that low specialisation stems from the production of customised goods in carpentry and welding, whereas grain milling products are standardised. Using our data, we also show that the production of customised goods entails significant communication and coordination costs between workers. This may make it difficult to “unbundle” a production process into separate tasks that can be allocated to distinct workers.
Figure 3: Differences in specialisation across sectors
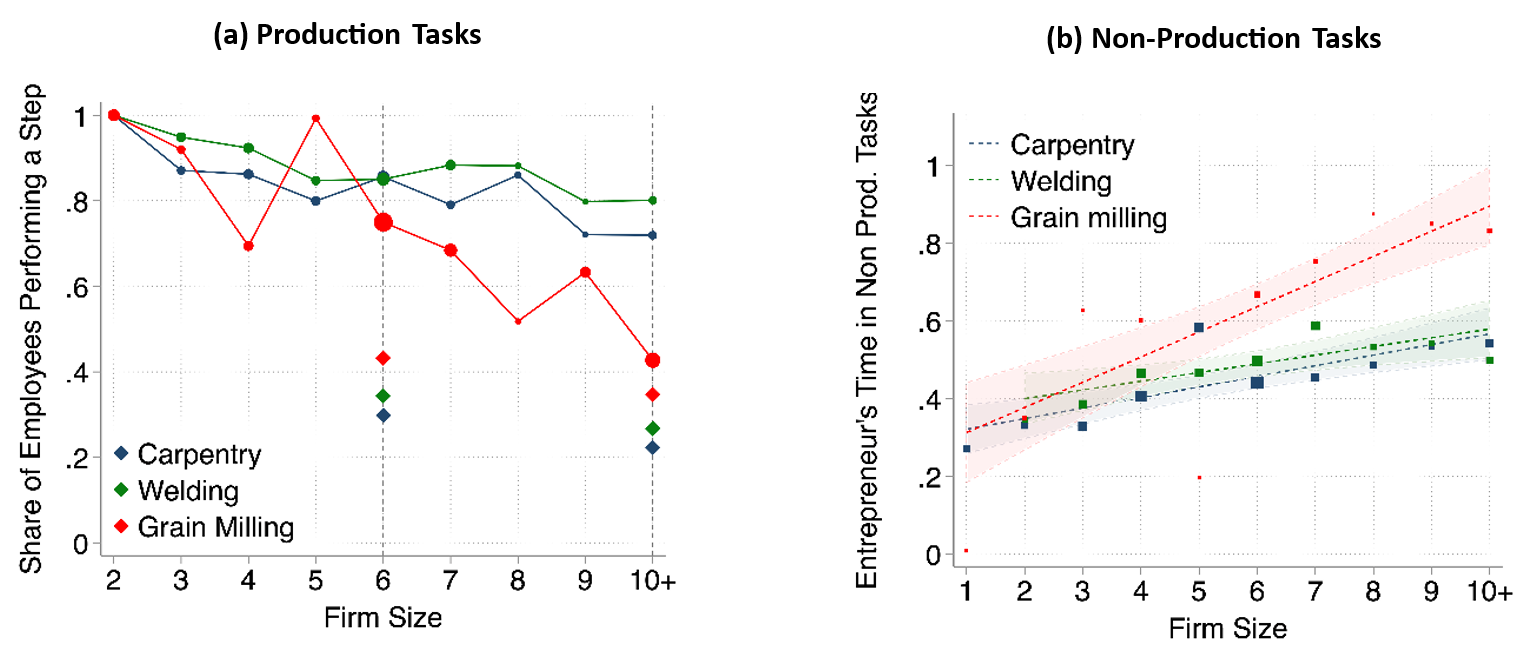
Notes: Panel (a) reports the share of employees working on the representative production step by sector. Panel (b) reports the share of time that entrepreneurs allocate to non-production tasks by sector.
Why do firms exist in this setting?
To what extent are individuals who work within a firm collectively more productive than if they worked independently? To answer this question, we design a model and estimate it with our data.
In our model, firms have two key roles: (i) they improve the economy-wide allocation of talent by letting the most skilled individuals self-select into entrepreneurship, and by allowing workers to specialise within firms across different tasks; (ii) they allow individuals to share a fixed production cost.
Bringing the model to the data, we find that carpentry and welding firms in Uganda face prohibitively high costs to specialise labour, and that entrepreneurs have limited other means to affect productivity independently of specialisation (e.g., brand reputation has only a limited role in this setting). Overall, our estimated economy is close to “self-employment within the firm” - a benchmark in which firms are not effective vehicles to leverage entrepreneurial talent and the productivity of each worker is the same, irrespective of the ability of the entrepreneur they work for. Thus, the only reason why firms exist in this benchmark is to share fixed costs, such as expensive production machines.
Interventions to help firms hire more workers are less effective if firms do not specialise
A key takeaway from our work is that the internal organisation of labour impacts the productivity gains from expanding firm size. In Figure 4, we show the impact of a policy that reduces the cost of hiring more workers under three different values of the costs of specialisation. These include the value that we estimate in carpentry and welding firms (in blue), a polar case of specialisation costs so high that there is zero specialisation (in black), and a lower value of specialisation costs corresponding to how grain milling firms operate (in red). The graphs show that when it’s costly to specialise, these interventions have comparatively lower returns.
Figure 4: Aggregate effects of changing the hiring cost

Notes: This figure shows how average firm size (panel a) and aggregate productivity (panel b) vary with changes in hiring costs. Each line corresponds to different values of the costs of specialisation (denoted by κ).
Policy implications: We need to help firms become scalable organisations
Our findings emphasise the importance of fostering scalable organisations: helping firms to hire more workers is not enough; we also need to change the way firms operate to make the business model more scalable in the first place. But how can we achieve this? Both demand-side and supply-side approaches may be important. Demand-side policies that connect firms to larger markets or promote product standards (see Goldberg and Reed 2022) could enhance labor specialisation (and therefore scalability) by fostering standardisation. Interventions that help firms build marketing skills and brand reputation, or that facilitate labour specialisation within and across firms (see Anderson and McKenzie 2022) may also be promising avenues to allow entrepreneurs to better leverage their talent and create scalable organisations.
References
Anderson, S J and D McKenzie (2022), "Improving business practices and the boundary of the entrepreneur: A randomized experiment comparing training, consulting, insourcing, and outsourcing." Journal of Political Economy, 130(1): 157-209.
Bassi, V, J H Lee, A Peter, T Porzio, R Sen, and E Tugume (2023), "Self-employment within the firm" (No. w31740). National Bureau of Economic Research.
Goldberg, P K and T Reed (2022), "Demand-side constraints in development: The role of market size, trade, and (in) equality." Yale University Working Paper, New Haven, CT.
Hsieh, C T and B A Olken (2014), "The missing “missing middle”." Journal of Economic Perspectives, 28(3): 89-108.
Jayachandran, S (2021), Microentrepreneurship in developing countries. Handbook of labor, human resources and population economics, 1-31.
Quinn, S and C Woodruff (2019), "Experiments and entrepreneurship in developing countries." Annual Review of Economics, 11: 225-248.